Construction continues
- Marc S. Tremblay
- Mar 17, 2024
- 4 min read
Updated: Jan 16
I'm happy to report that construction is continuing at the Grove, despite a few cold rainy days and me not being able to spend as much time there as I'd like.

As I've said several times, I'm grateful to Steve and his crew for their diligent work and for coordinating efforts with other important contractors, like Plumber Jeff and Electrician Dean. Chris the Roofer also started working on installing a new metal roof, so it's been a busy worksite. On one of the days I went to the Grove to "supervise", I couldn't park in the driveway...
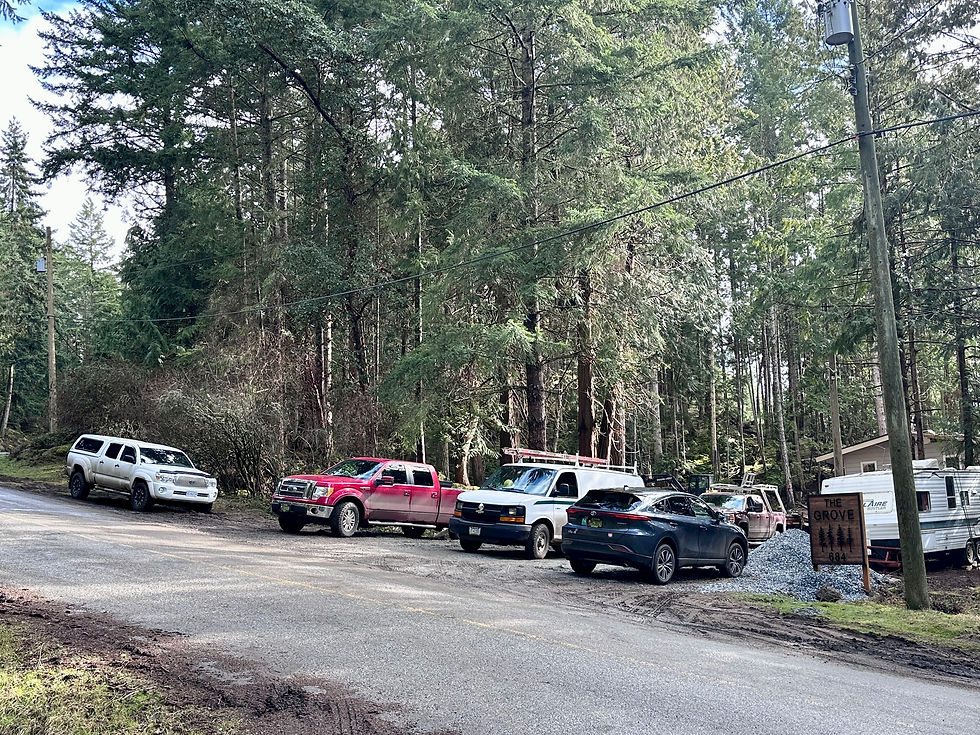
After the slab was poured and set, workers continued to work on framing, plumbing and electrical. From a framing point of view, lots of work went into framing the lower lever, where we'll have a 1-bedroom suite, a flex room, a bathroom, a storage room and the mechanical room. Steve and his crew also build the staircase and continued to frame out the Office on the upper level.
We're also well-passed the rough-in portion of the electrical and plumbing installations, with electrical outlets and wires going every which way, while water lines and drains are in place waiting for CRD inspection, this coming week.
Backfilling around the ICF foundations was a bit of challenge. The ground around the house is silty-sandy, with a high clay content. With all the rain we received, excavator Matt and Contractor Steve thought that we should put even more gravel in the trench on top of the perimeter drains. Little did we know, there's a bit of a shortage of gravel and it's pretty expensive to truck it to Mayne Island. So, in lieu of using only small draining gravel, Matt suggested that we use larger fill instead of just pushing the wet-silty-sandy-clay mixture back in the trench, which made sense to me.
We ordered the "8-minus" product, meaning that all rock pieces should have been about 8 inches of smaller. In the end, the available product on Mayne was much larger than that, with some pieces as big as 18-20 inches. Those are some pretty big and heavy rocks!
I was afraid that even if Paul, Matt's employee, used all the care in the world, that a big rock could hit the foundation wall and either damage the foundation, or, puncture the peel-and-stick membrane and dimple board installed for waterproofing. To make sure that didn't happen we purchased 25 sheets of 1/2 inch plywood and installed it against the foundation wall to protect it. It's not ideal, and the plywood will eventually rot in place, but by then, the big rocks and other smaller pieces will have settled, gently we hope, maintaining the integrity of the walls' water repellent system.
The top layer installed on top of the rock fill is native soil. Hopefully, with proper landscaping and native grasses, the water will seep-in and drain away as planned. Right now, it looks and feels like we have a top layer of impermeable Gore-Tex, which is pooling water, making big mud puddles and quicksand.

While on the subject of water, our water-well is over 30 years old. The old set-up used an external spa pump and air tank to make the well flow. Before we started preparing the lot for the house to arrive, it worked well and the water quality was excellent, but I felt we should upgrade and modernize it as part of this project. I hired the company Wellmaster Pumps to come install a submersible pump and make other changes.
They installed a "pitless adapter", among other improvements, which reduced the footprint of the wellhead. The other advantage is that the water line is sufficiently buried to prevent frost damage, and now, we have a shiny new blue wellhead!
I made myself useful by researching where we could purchase windows and doors. With Cassia's help, we narrowed it down to Van Isle Windows and Starline Windows. We visited both stores to get a feel for each of the vendors' windows. Both Cassia and I felt it was no contest: 1. Van Isle's windows were better quality; 2. the employee, Ted, was more knowledgeable and helpful; 3. and their prices were about 40% cheaper than Starline's. It was an easy decision. We purchased nine new windows for the house, six to be installed downstairs, three upstairs in the Office.
I single-sourced the doors based on recommendations I received form a construction expert. Doors were purchased from Windsor Plywood. Buying doors was a bit more complicated than buying windows. Well, complicated may not be the right word, but there are more options to consider:
what height and width?
should the door swing left or right?
should it swing in or out?
with a solid core or hollow core?
pre-hung or not?
if pre-hung, on what size jam, 4 and 9/16 or 6 and 9/16?
single or double drilled?
with silver, brushed nickel or gold coloured hinges?
Manager Cindy was incredibly helpful, and patient, while we worked through all the new doors required for our project. In all, we purchased 13 doors.
The windows were picked up and delivered to our worksite by the Mayne Island Freight company, which is operated by the Home Hardware store. It's quite a bit more affordable to use them to pick up and deliver freight as part of their regular Thursday Victoria-runs, compared to using the manufacturers' delivery service.
So far, only the exterior doors were picked up from Windsor Plywood. We're waiting until the drywall is hung before we bring the interior doors, that way, they're not in the way of the workers moving big sheets of drywall around.
Finally, on one of our recent visits, Keiver, Cassia, Airi and her sister Mahalo came out to help clean-up the construction debris. We had a great day building a bonfire and Dana even test-drove the bathtub!
Next up: a new metal roof, siding, drywall, flooring, the water-catchment system and septic system.
Comments